HOLONOMIC DRIVE PLATFORM FOR MOBILE ROBOTS
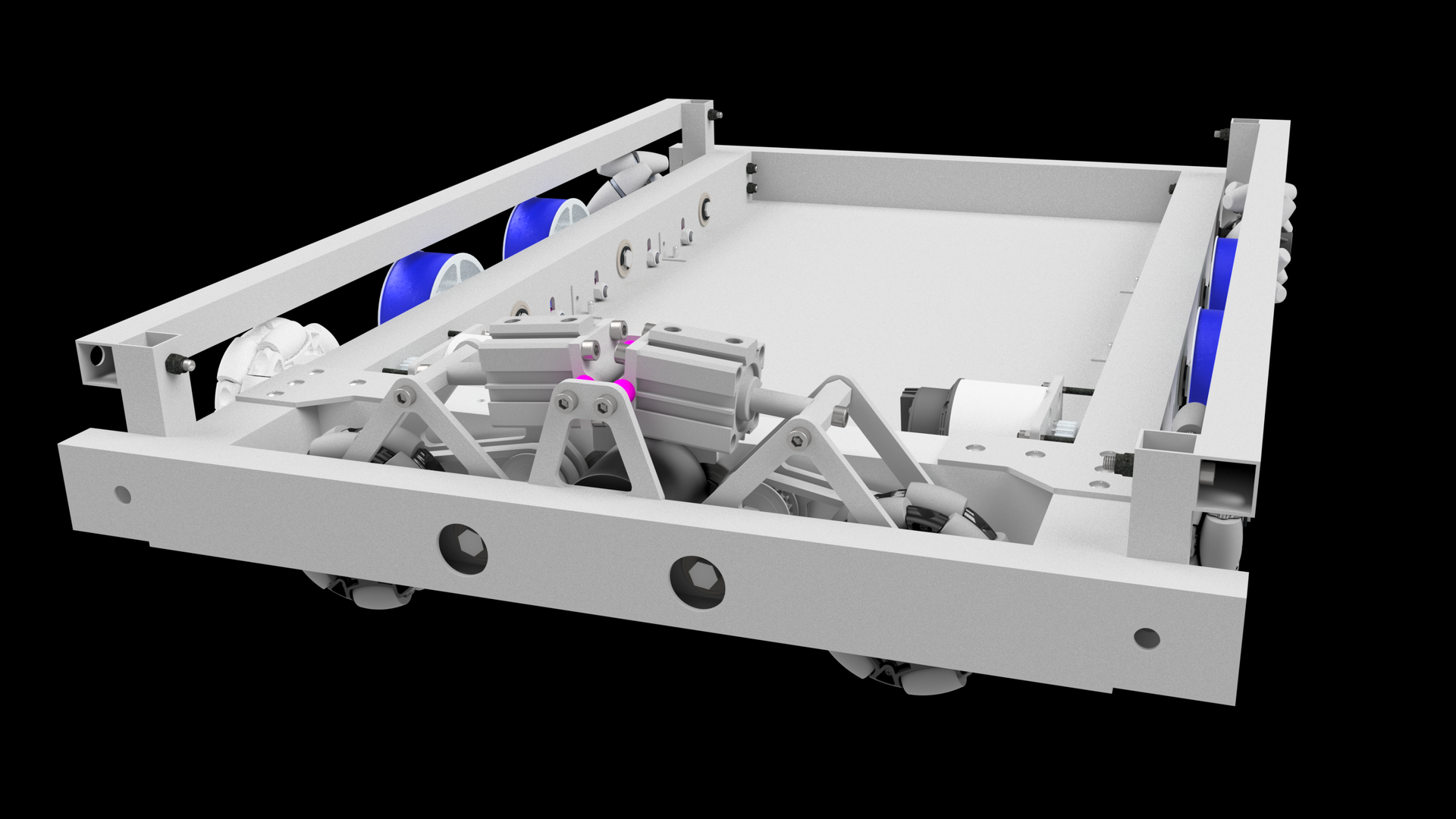
The Goal of the holonomic drive project was to create a cost-effective approach to acheiving holonomic (omnidirectional) motion on competition robots, more specifically, FRC robots, which weigh over 50kg and move around a basketball court-sized arena.
Before continuing, I suggest taking a look at This Page, which explains a bit more about the FIRST Robotics Competition (FRC) which will add context to this project.A typical differential-drive (also known as "skid steer") robot is restricted to moving forwards and backwards, as well as rotating. In a competitive environment, holonomic drivetrains have the advantage, as they are able to maneuver around the field more easily. The method for acheiving this is using four independant mechanum wheels, which use rollers at a 45 degree angle to create an off-axis force vector. The disadvantage of this approach is the reduction in traction, resulting in lower acceleration and being pushed around by a robot from the opposing team.
These problems can be solved in a number of ways, two of which are explored in this project.
The project was first conceived in 2020 with this design of a "swerve drive" (picture a castor wheel that is powered on both axes). Swerve drives offer far greater speed and traction over mechanum designs due to not relying on slippage to create sideways forces, at the cost of greater complexity.
Seen in the figure is one of four swerve modules that would be mounted on each corner of a platform. The 775 DC motor on the right is used to steer the wheel assembly through a belt reduction and an absolute encoder, whilst the brushless NEO motor (top of main assembly) transmits drive power to the wheel through a series of gears and a shaft that is coaxial to the axis of rotation. The coaxial design eliminates the need of a slip ring, since both motors can be stationary.
Unfortunately, this iteration never came to fruition due to cost and time limitations.
Towards the end of 2022, I revisited the project, this time with a friend who shared similar ambitions. We decided to completely rethink the design from the ground up- Instead of creating the entire drive platform, which would have an unknown reliability during competition, We would devise a single module that attaches to a proven skid-steer drivebase.
The new design is a hybrid between common skid-steer and mechanum. Two pneumatic cylinders deploy or retract two "omni" wheels, which are wheels with perpendicular rollers, allowing them to slip given non-planar motion. In the retracted state, the the robot has the speed and traction of skid-steer. When extended, only the rear omni wheels and the foremost mechanum wheels contact the ground, behaving similar to a mechanum drivetrain.
The design has similar complexities to the swerve module - in order to transmit power to the omni wheels, a sigle shaft serves as both a dead axle for the pivot, and a live axle for power transmission.
To verify the design works as expected, we created a simplified module that attaches to the previous year's competition robot. The video speaks for itself:
This was as far as the project went- Due to an unexpected source of funds, we were able to purchase Off-The-Shelf swerve modules, which by this time had become more accessible to medium-budget teams.
That being said, as competition robotics continues to become more prevalant in WA schools, we can expect to see an adaptation of the project in the not-so-distant future.